Ideas
Product design? It’s not about the shape, we are looking for solutions. It is a path to products which are 100 % functional, as easy as possible to produce and have reasonable aesthetics.
The result is products which will last. They will serve not only you but also the following generations. They resist current trends because their creators didn’t bet on the first impression.
Make
How to leave the smallest possible carbon footprint? Not to give up control of your own production. To know, from where and how raw materials are imported, in what environment they are produced, to use environmentally friendly technologies.
We use our own thermally modified wood, use a biomass heating system and recuperation units for heating our production halls, and our cars drive on alternative fuels. Production scraps are not seen as waste but as a source for new products.
Products
Thanks to their design, our products age gracefully. Thanks to their elaborate construction and the technologies used, they don’t get run-down. We take extra care that our products don’t lose a bit of their functionality with every new season.
After sandblasting, metallic parts are galvanized and coated with a quality finish. The textiles we use are UV resistant and we prefer to make firm connections than use screws where possible.
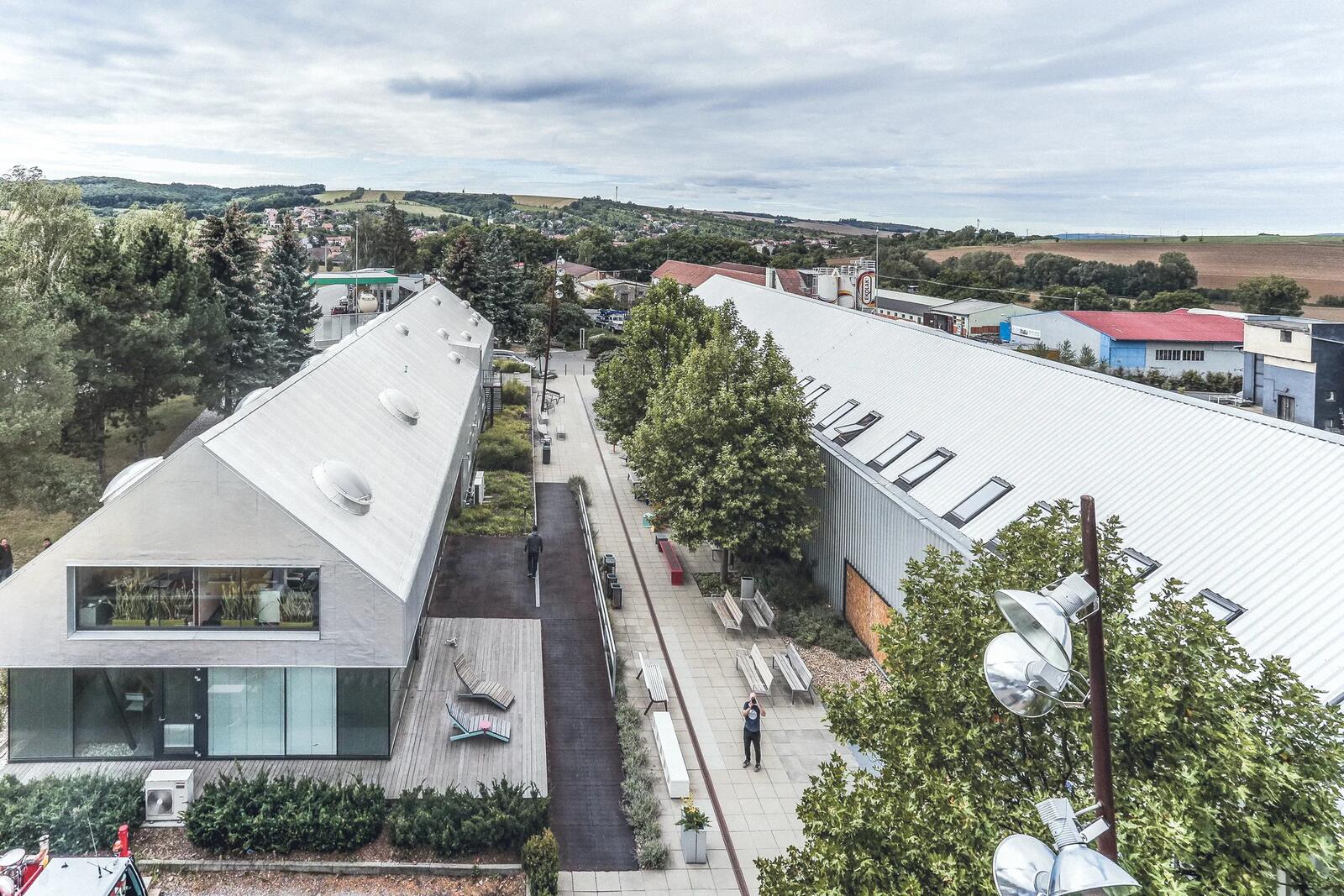
Principle ECO 2.0
Ecological and economical at the same time
In all phases, from the development through the choice of materials and technological processes up to the logistics, sustainability is the crucial factor for us.
We try to minimise the negative impact on the environment, while at the same time not jeopardizing the stability of the company. The ecological and economical aspects must be considered simultaneously. This is what we call ECO 2.0.
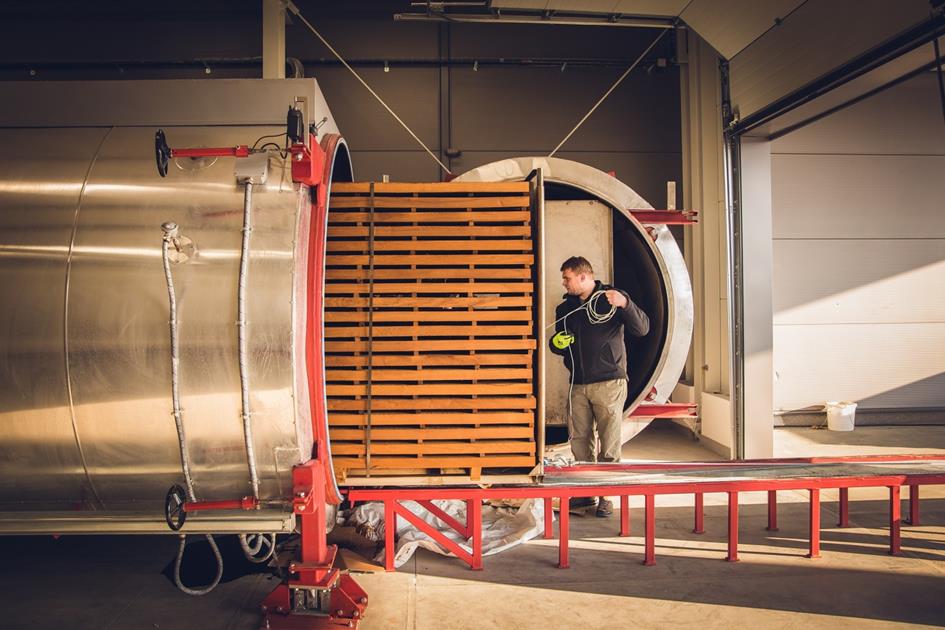
Tropical woodmade in Bílovice
Wood and us? Several hundred tons every year. Including tropical woods. Our effort to eliminate the impact of wood harvesting and transportation on the environment has led us to the process of thermal modification of wood.
During the application of this method, common European wood types gain properties similar to tropical wood. Instead of importing wood from, let’s say, South America, why not use a pine growing nearby?
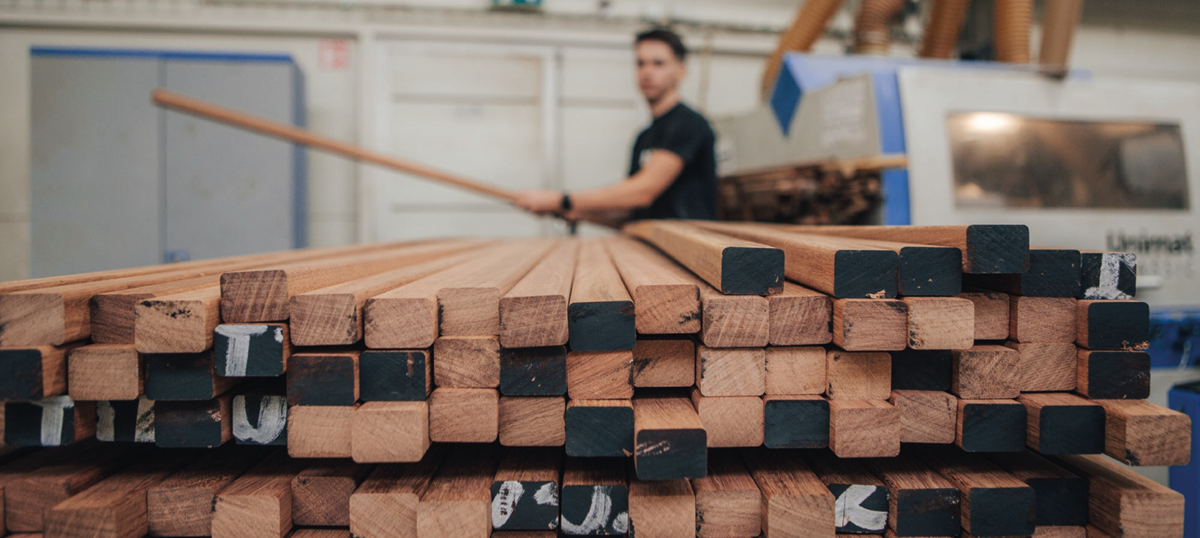
Materials?We are picky
We choose the wood for our products carefully and look at the FSC® certification - all the products are manufactured through the FSC certificate (FSC-C011999). Therefore, we can guarantee that the wood we use comes from forests which are responsibly managed with regard to the environment and nature.
By buying FSC labelled products, you help to protect the forests. But we are also responsible when choosing the textiles – for example our favourite Crevin is produced from recycled materials.
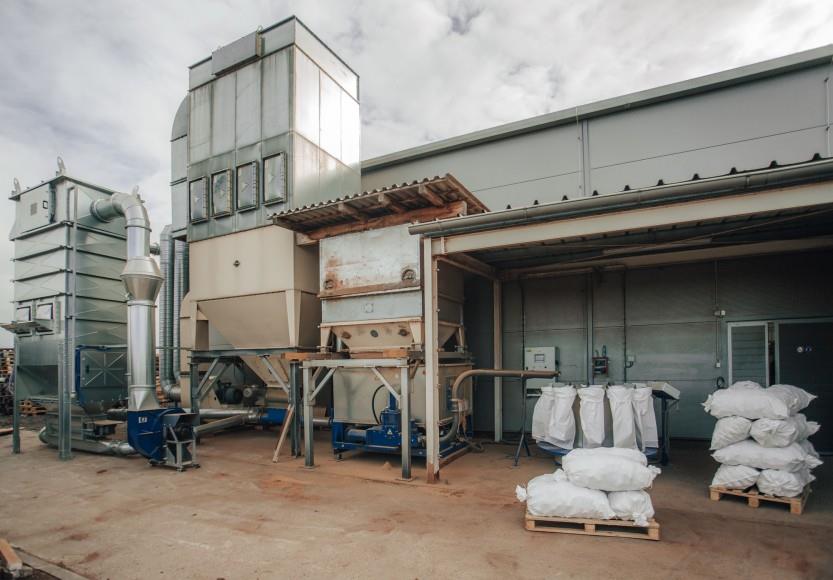
How do we heat?Leftovers
Waste heat and scraps from wood production. These are the heat sources for most of the production spaces at Egoé. The goal is not to throw unnecessary money or carbon dioxide emissions out of the window.
The two new halls with a floor area of 3,000 square metres are unique only at the second glance. The heating is provided by a wood gasifier. The fuel are the remnants from the wood production which would otherwise have no other further use.
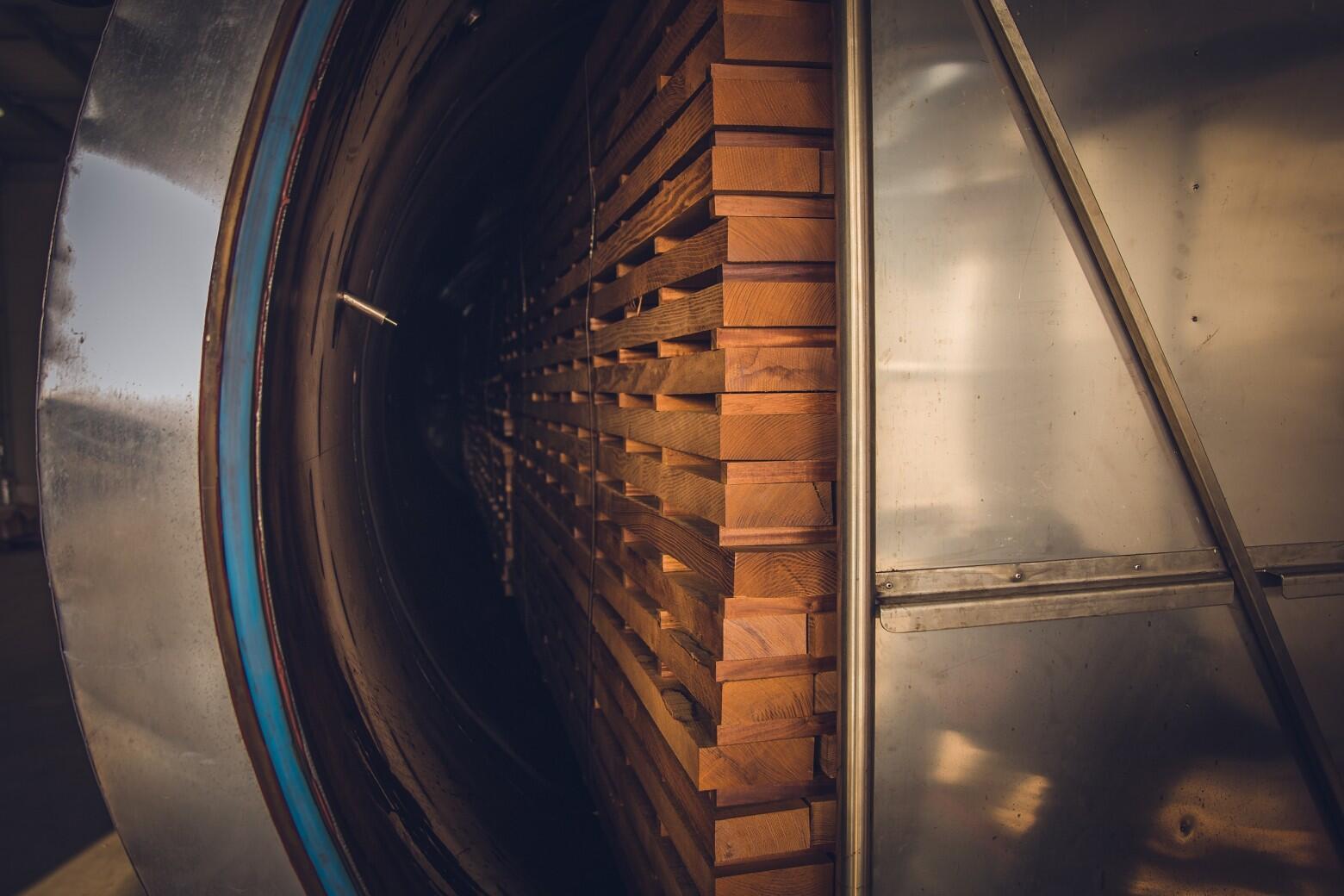
Thermization line
The line for thermal modification on the premises of Egoé was commissioned in February 2022 and has a capacity of ten square metres. The most common wood types for processing are ash, pine, larch and spruce. The wood is heated at temperatures between 170 to 220 °C, with vacuum, steam and water being used during the process. Thus, we can reduce the consumption of tropical wood and the carbon footprint of our final products.
Tons of oxide emissions saved
Cars and handling vehicles run on compressed natural gas instead of oil and plug-in hybrids. In addition, there is a company filling station and the first public charging station in the region. Our company fleet has many vehicles which run on alternative fuels. We have been buying them for many years. Thus, we save 13,500 kg CO2 and 152,000 kg NOx every year.
We retain and don’t let go
Water doesn’t have it easy with us. Who knows, it might want to go elsewhere. But it is not possible. On the company premises in Bílovice 519, its service will be long. Especially regarding rainwater falling on our roofs and hard surfaces. Instead of the sewage system, it is directed to our pond. It fulfils three functions. Firstly, it makes our premises nicer. Secondly, we use it to water our fruit tree orchard. And thirdly, it is the main source of fire water.
White Carpathians and Angola.
We are not thrifty when it comes to planting
The salvage logging in the Czech White Carpathians mountains left a two-hectare bald area. We bought it and gradually planted 14,000 new trees there. And keep taking care of the new growing forest. Planting trees has a deeper meaning in our case. We planted more than 3,000 of them in Angola, Africa. Our premises in Bílovice boasts an orchard. We work with wood and are settling the score by these efforts. In a nutshell, a tree for a tree.
When scrap makes sense
Construction sets, play elements, educational games. These all can be created from a pile of scrap wood. What is needed is the right idea and the will to use everything. Didawood is what we call this meaningful project. However, didawood is not only about our wood or scrap wood. We have managed to persuade other companies to join us. They deliver for example cardboard waste or textiles which we use for packaging or accessories. Circular economy in practice.
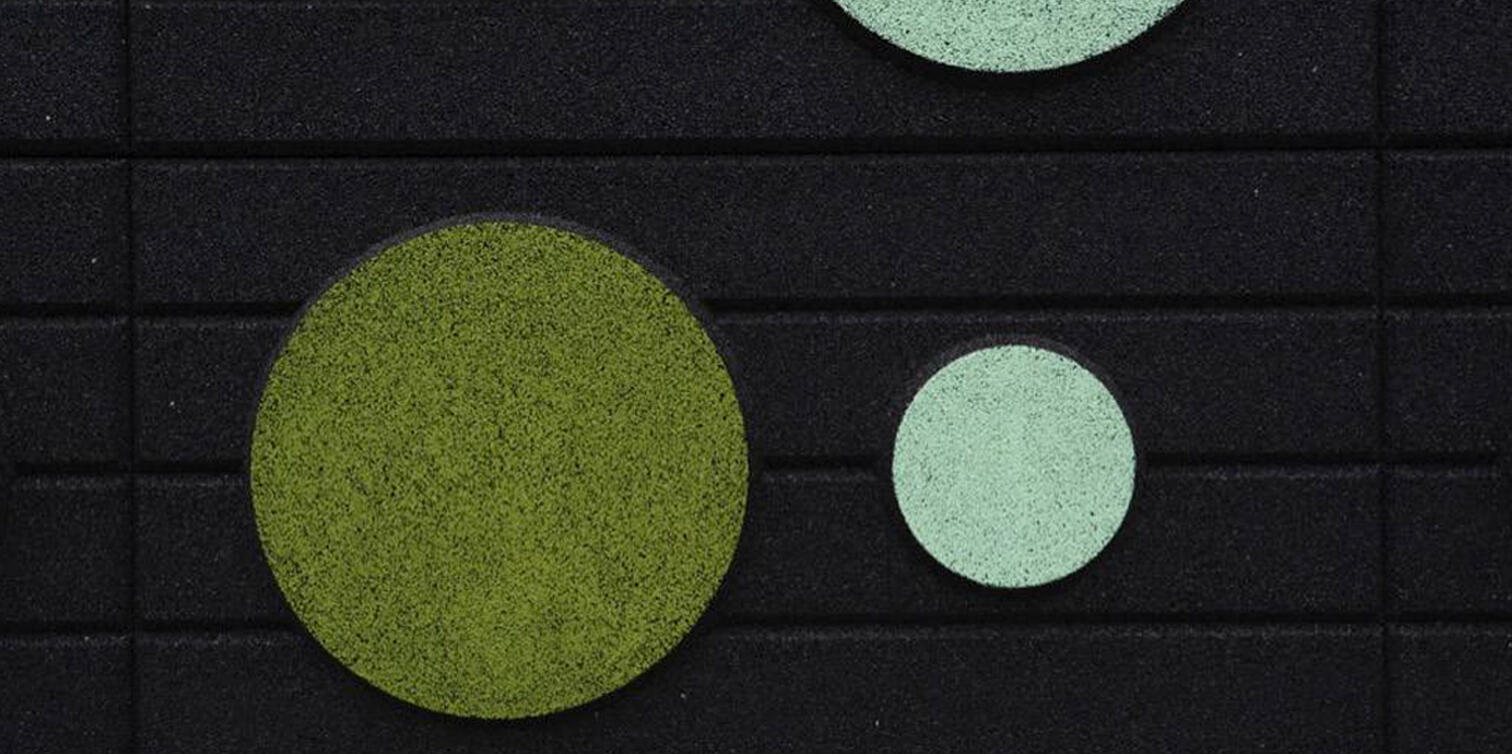
Sustainability
When black is actually green
Old tyres instead of gravel and cement
Noise barriers. Hundreds of kilometres along highways, roads and railways. Made mostly from concrete. And in between, shining black or grey sections. By Egoé. From old tyres. And PET bottles as well. The noise barrier noba is actually green. The basic material for its production are products at the end of their lifespan – used tyres. Instead of being stored at a dump or burned, they gain a second life.
Ingredients? Five tyres plus five PET bottles
The absorption panels for the noba noise barrier are made from recycled rubber. For the production of one square metre, five personal car tyres are needed. Where the noise barrier features a final layer of textile, additional five 1,4 litre PET bottles were used during the production.
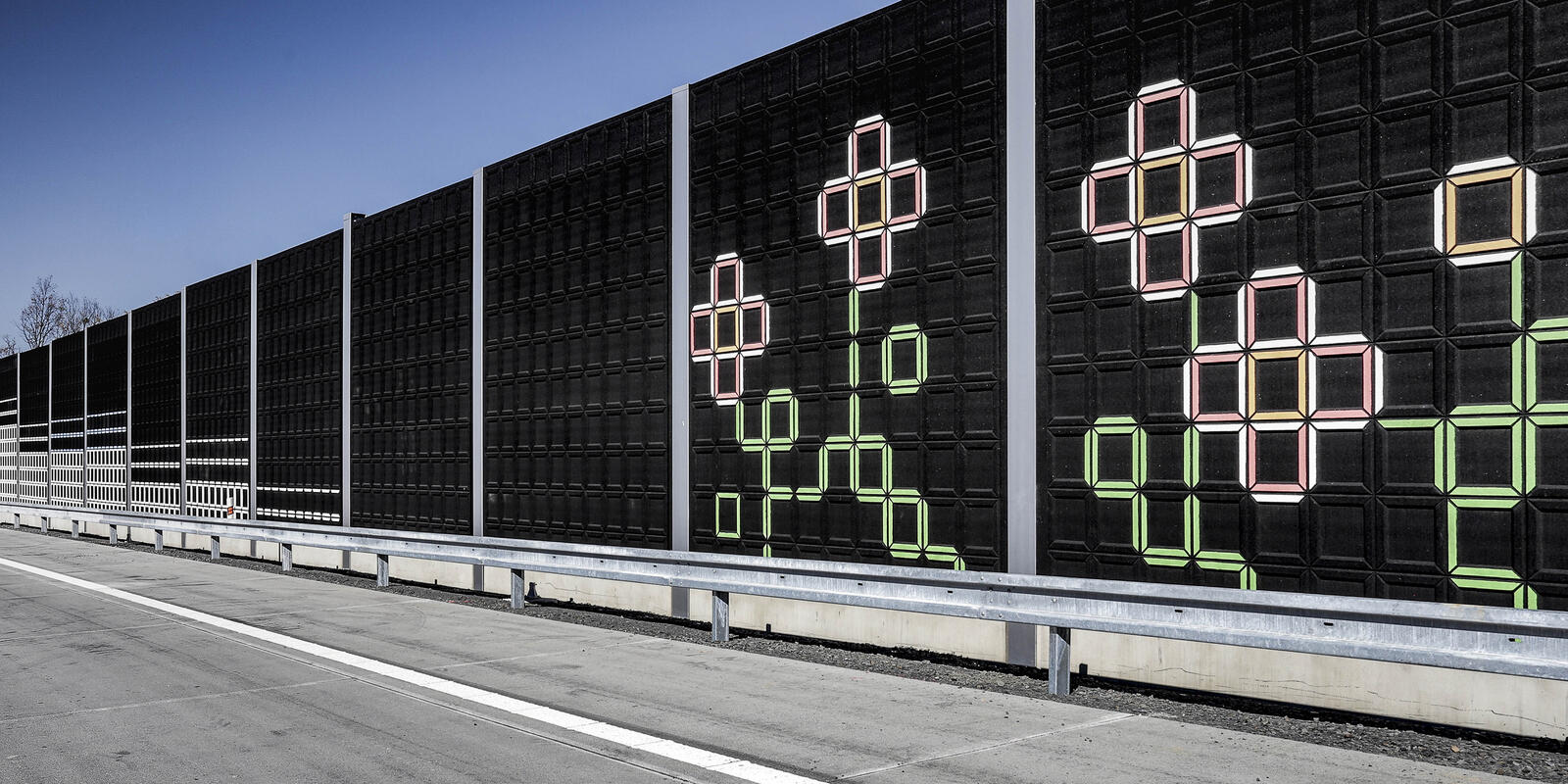
Noise barrier noba as an example of a circular economy
Road noise barriers are mostly made from concrete elements. The basic raw materials, cement and gravel, are not renewable sources and the production of the noise barrier consumes much energy. Noba, on the contrary, uses waste products and extends their usage life. The whole system consists mostly of recycled materials which can be recycled again once the lifespan of the barrier reaches its end.